Vacuum Nozzle Pressure Sensor Control Application for Semiconductor Die Bonder
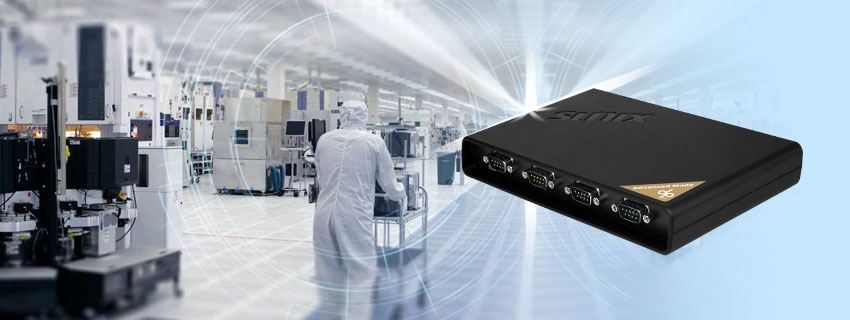
A semiconductor manufacturer, who we are providing consultation on helping them to improve their production efficiency while reducing overall maintenance cost, cover a vast area of products and services in semiconductor and optoelectronics sectors to establish complementary to a comprehensive product line. In conventional operation, onsite personnel are needed to monitor the pressure status from the semiconductor die bonder. If the pressure is too strong or too weak on the die bonder’s nozzle, it will case damages to the die while picking them up which result in big losses. In this smart factory and big data era, the production and machine status and data can be recorded and transmitted in real-time to the cloud or central control for predictive maintenance analysis to increase productivity and reduce maintenance costs.
Prior to Consultation – Insufficient Communication Port in the Machine
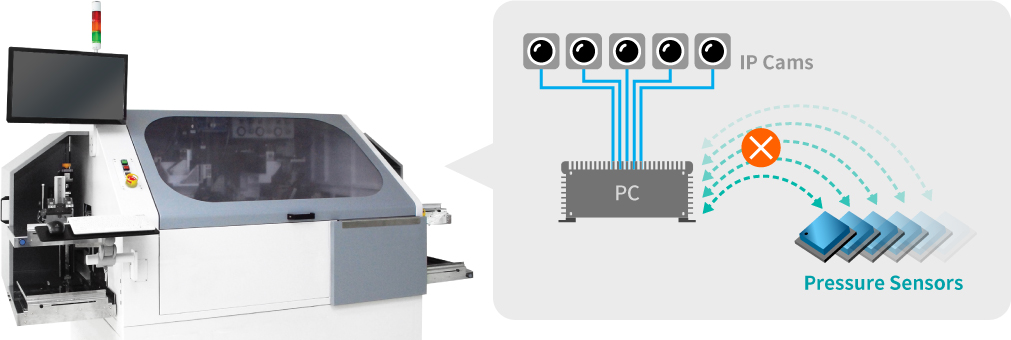
Post Consultation – DevicePort Solution
Eliminate wiring through network expansion
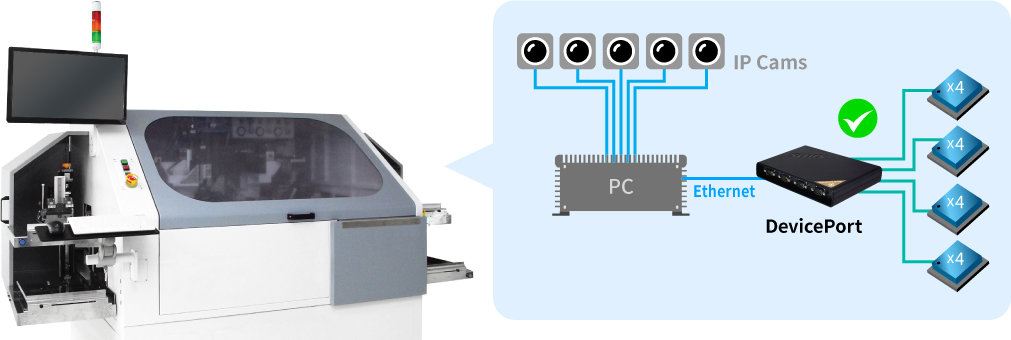
DevicePort allows you to eliminate the system specification limitation on expanding add-on cards in the setup; freely expand serial ports, monitoring and manage data remotely. Obtaining the key and move towards smart manufacturing!
Benefits after the implementation
Solve customer system expansion issues
Eliminate system limitation on ports expansion, allowing users the freedom to expand serial ports as needed for their specific application
Remote monitoring of air pressure
Traditionally, personnel are needed to be present onsite to monitor air pressure of each nozzles, and make necessary adjustment constantly. If the pressure is too strong or too weak, it will cause damages to the ejector pin while picking up the die which will cause financial losses. After implementing SUNIX DevicePort solution, real-time monitoring and parameters adjustment can be made remotely, and enable automatic monitoring and operation implementation for preventive maintenance to reduce production losses.
Product stability
After over half a year testing with our DevicePort solution, SUNIX product has proven to be a big improvement over their previous solution; and shown craftmanship of stability, quality, and post sales customer services.
Solutions
AI Inference
Banking
Restaurant / POS
Medical
Security
Factory Automation
CANbus Application
Transportation
Kiosk and Self-service
Public Utilities
Factory Automation
-
FOUP Nitrogen Filling Machine Monitoring Management Application
-
Vacuum Nozzle Pressure Sensor Control Application for Semiconductor Die Bonder
-
Factory Test Machine Virtualization Management System Construction
-
Easily Monitor and Maintain Automated Manufacturing Systems with Industrial Device Servers from SUNIX
Vacuum Nozzle Pressure Sensor Control Application for Semiconductor Die Bonder
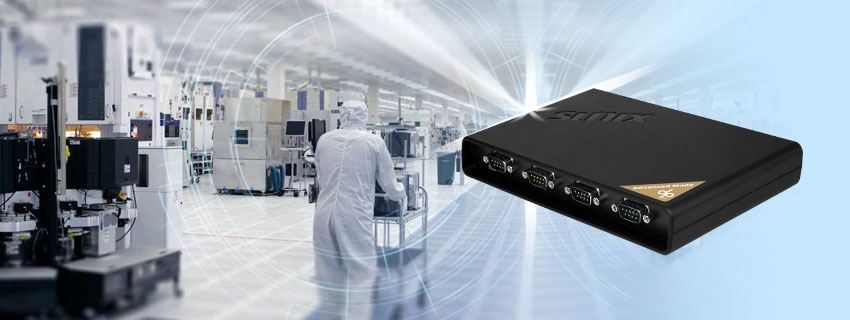
A semiconductor manufacturer, who we are providing consultation on helping them to improve their production efficiency while reducing overall maintenance cost, cover a vast area of products and services in semiconductor and optoelectronics sectors to establish complementary to a comprehensive product line. In conventional operation, onsite personnel are needed to monitor the pressure status from the semiconductor die bonder. If the pressure is too strong or too weak on the die bonder’s nozzle, it will case damages to the die while picking them up which result in big losses. In this smart factory and big data era, the production and machine status and data can be recorded and transmitted in real-time to the cloud or central control for predictive maintenance analysis to increase productivity and reduce maintenance costs.
Prior to Consultation – Insufficient Communication Port in the Machine
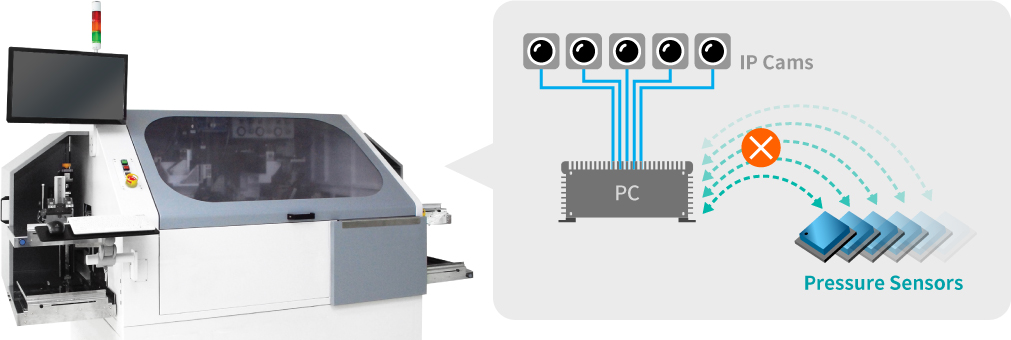
Post Consultation – DevicePort Solution
Eliminate wiring through network expansion
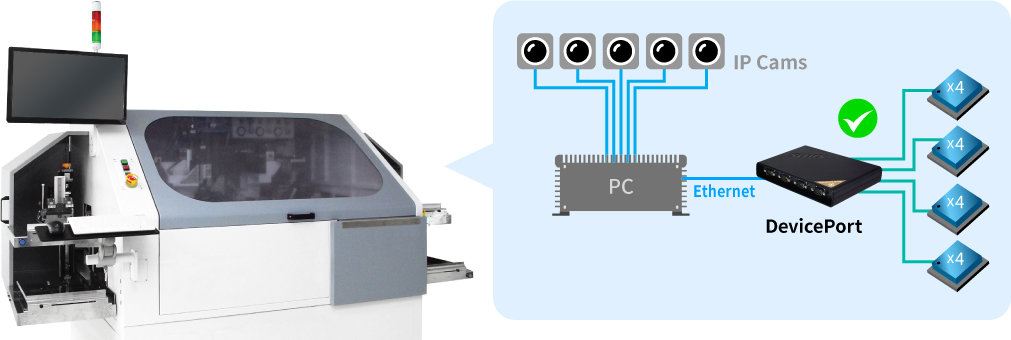
DevicePort allows you to eliminate the system specification limitation on expanding add-on cards in the setup; freely expand serial ports, monitoring and manage data remotely. Obtaining the key and move towards smart manufacturing!
Benefits after the implementation
Solve customer system expansion issues
Eliminate system limitation on ports expansion, allowing users the freedom to expand serial ports as needed for their specific application
Remote monitoring of air pressure
Traditionally, personnel are needed to be present onsite to monitor air pressure of each nozzles, and make necessary adjustment constantly. If the pressure is too strong or too weak, it will cause damages to the ejector pin while picking up the die which will cause financial losses. After implementing SUNIX DevicePort solution, real-time monitoring and parameters adjustment can be made remotely, and enable automatic monitoring and operation implementation for preventive maintenance to reduce production losses.
Product stability
After over half a year testing with our DevicePort solution, SUNIX product has proven to be a big improvement over their previous solution; and shown craftmanship of stability, quality, and post sales customer services.
Solutions
AI Inference
Banking
Restaurant / POS
Medical
Security
Factory Automation
CANbus Application
Transportation
Kiosk and Self-service
Public Utilities
Factory Automation
-
FOUP Nitrogen Filling Machine Monitoring Management Application
-
Vacuum Nozzle Pressure Sensor Control Application for Semiconductor Die Bonder
-
Factory Test Machine Virtualization Management System Construction
-
Easily Monitor and Maintain Automated Manufacturing Systems with Industrial Device Servers from SUNIX
Vacuum Nozzle Pressure Sensor Control Application for Semiconductor Die Bonder
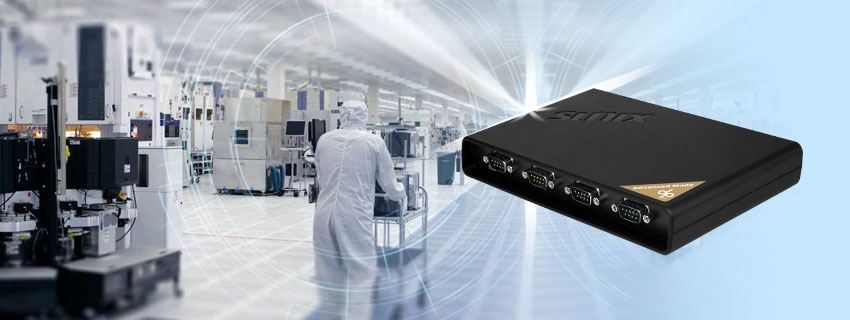
A semiconductor manufacturer, who we are providing consultation on helping them to improve their production efficiency while reducing overall maintenance cost, cover a vast area of products and services in semiconductor and optoelectronics sectors to establish complementary to a comprehensive product line. In conventional operation, onsite personnel are needed to monitor the pressure status from the semiconductor die bonder. If the pressure is too strong or too weak on the die bonder’s nozzle, it will case damages to the die while picking them up which result in big losses. In this smart factory and big data era, the production and machine status and data can be recorded and transmitted in real-time to the cloud or central control for predictive maintenance analysis to increase productivity and reduce maintenance costs.
Prior to Consultation – Insufficient Communication Port in the Machine
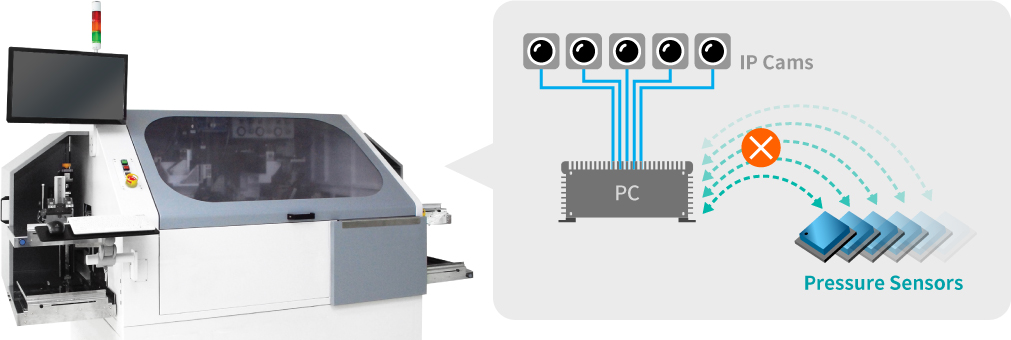
Post Consultation – DevicePort Solution
Eliminate wiring through network expansion
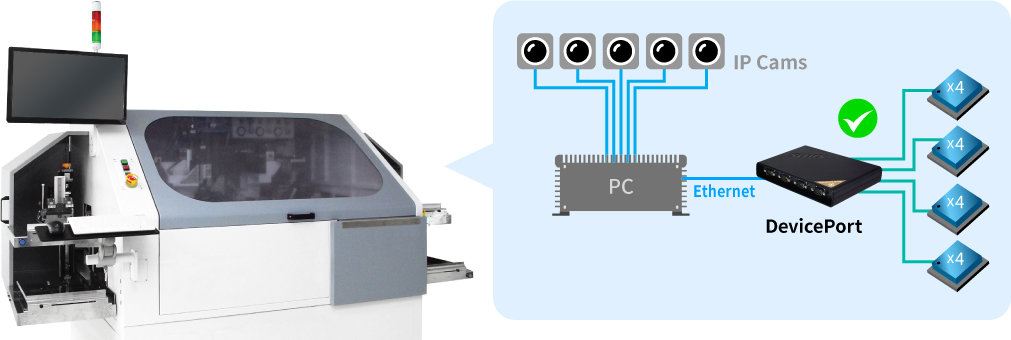
DevicePort allows you to eliminate the system specification limitation on expanding add-on cards in the setup; freely expand serial ports, monitoring and manage data remotely. Obtaining the key and move towards smart manufacturing!
Benefits after the implementation
Solve customer system expansion issues
Eliminate system limitation on ports expansion, allowing users the freedom to expand serial ports as needed for their specific application
Remote monitoring of air pressure
Traditionally, personnel are needed to be present onsite to monitor air pressure of each nozzles, and make necessary adjustment constantly. If the pressure is too strong or too weak, it will cause damages to the ejector pin while picking up the die which will cause financial losses. After implementing SUNIX DevicePort solution, real-time monitoring and parameters adjustment can be made remotely, and enable automatic monitoring and operation implementation for preventive maintenance to reduce production losses.
Product stability
After over half a year testing with our DevicePort solution, SUNIX product has proven to be a big improvement over their previous solution; and shown craftmanship of stability, quality, and post sales customer services.
Solutions
AI Inference
Banking
Restaurant / POS
Medical
Security
Factory Automation
CANbus Application
Transportation
Kiosk and Self-service
Public Utilities
Factory Automation
-
FOUP Nitrogen Filling Machine Monitoring Management Application
-
Vacuum Nozzle Pressure Sensor Control Application for Semiconductor Die Bonder
-
Factory Test Machine Virtualization Management System Construction
-
Easily Monitor and Maintain Automated Manufacturing Systems with Industrial Device Servers from SUNIX
Vacuum Nozzle Pressure Sensor Control Application for Semiconductor Die Bonder
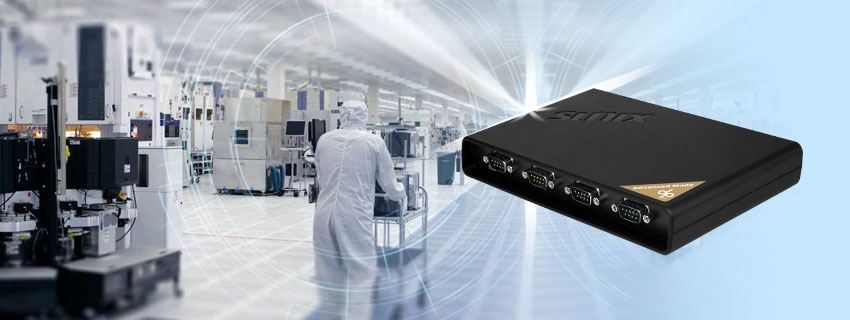
A semiconductor manufacturer, who we are providing consultation on helping them to improve their production efficiency while reducing overall maintenance cost, cover a vast area of products and services in semiconductor and optoelectronics sectors to establish complementary to a comprehensive product line. In conventional operation, onsite personnel are needed to monitor the pressure status from the semiconductor die bonder. If the pressure is too strong or too weak on the die bonder’s nozzle, it will case damages to the die while picking them up which result in big losses. In this smart factory and big data era, the production and machine status and data can be recorded and transmitted in real-time to the cloud or central control for predictive maintenance analysis to increase productivity and reduce maintenance costs.
Prior to Consultation – Insufficient Communication Port in the Machine
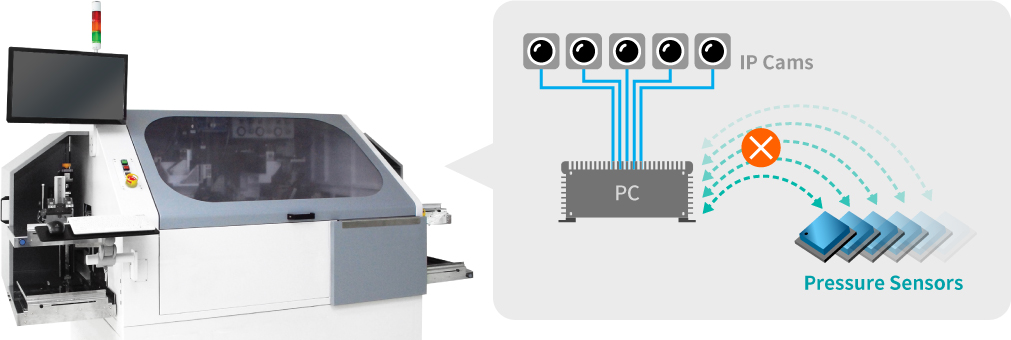
Post Consultation – DevicePort Solution
Eliminate wiring through network expansion
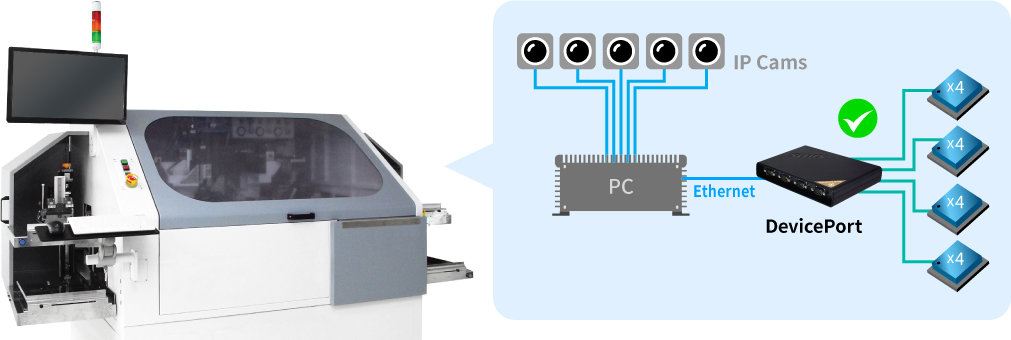
DevicePort allows you to eliminate the system specification limitation on expanding add-on cards in the setup; freely expand serial ports, monitoring and manage data remotely. Obtaining the key and move towards smart manufacturing!
Benefits after the implementation
Solve customer system expansion issues
Eliminate system limitation on ports expansion, allowing users the freedom to expand serial ports as needed for their specific application
Remote monitoring of air pressure
Traditionally, personnel are needed to be present onsite to monitor air pressure of each nozzles, and make necessary adjustment constantly. If the pressure is too strong or too weak, it will cause damages to the ejector pin while picking up the die which will cause financial losses. After implementing SUNIX DevicePort solution, real-time monitoring and parameters adjustment can be made remotely, and enable automatic monitoring and operation implementation for preventive maintenance to reduce production losses.
Product stability
After over half a year testing with our DevicePort solution, SUNIX product has proven to be a big improvement over their previous solution; and shown craftmanship of stability, quality, and post sales customer services.
Solutions
AI Inference
Banking
Restaurant / POS
Medical
Security
Factory Automation
CANbus Application
Transportation
Kiosk and Self-service
Public Utilities
Factory Automation
-
FOUP Nitrogen Filling Machine Monitoring Management Application
-
Vacuum Nozzle Pressure Sensor Control Application for Semiconductor Die Bonder
-
Factory Test Machine Virtualization Management System Construction
-
Easily Monitor and Maintain Automated Manufacturing Systems with Industrial Device Servers from SUNIX